摘要
碳化硅FET已经在车载充电器(OBC)电路领域确立了自身地位,尤其是在电池工作电压超过500V的情况下。这些器件的低功率损耗使得穿孔封装和表面安装式封装都可以用于此应用。我们调查了这些封装选项的相对热性能,并证实了TO247-4L和D2PAK-7L选项可用于6.6 kW和22 kW充电器。
简介
碳化硅FET已经广泛应用于纯电动车(EV)的车载充电器(OBC)和直流转换器。它们在牵引逆变器中的使用也快速增长。由于开关速度比IGBT快得多,它们成为了系统总线电压超过500 V(如800 V)时的首选器件。在系统总线电压较低的PFC电路需要硬开关时,它们也是出色的选择,因为它们的二极管恢复性能比硅超结FET好得多,因而可以实现较高频率的开关和较低的损耗。最后,这些充电器日益增长的支持双向能量流动以允许能量从车辆传入电网的趋势也得到了这些宽带隙器件的此类属性的支持。
车载充电器会转换单相或3相交流电,将其输入直流轨,然后使用直流转换器为车辆电池充电。在充电模式下,前端充当整流器,并使用图腾柱PFC,或者在较高功率下充当有源前端。可以操作这些电路,使其让电流反向传输,也就是充当逆变器。为实现充电所选的直流转直流拓扑可以是LLC或CLLC类型,后者适合双向能量传输。直流轨还可以支持另一个功率较低的LLC转换器,为电动车中的12 V电子器件供电。如果不需要双向能量流,PFC整流器通常选择使用Vienna整流器。
SiC器件技术和封装选项
图1显示的是商用单极功率半导体的先进性。过去十年中器件技术的持续进步造就了第四代SiC JFET和SiC FET(共源共栅结构),在图中以蓝色符号表示。给定额定值下的低RdsA可以在相同的封装中实现更低的电阻。它还允许以较小的晶粒体积和电容实现给定导通电阻,从而也实现更低的开关损耗。
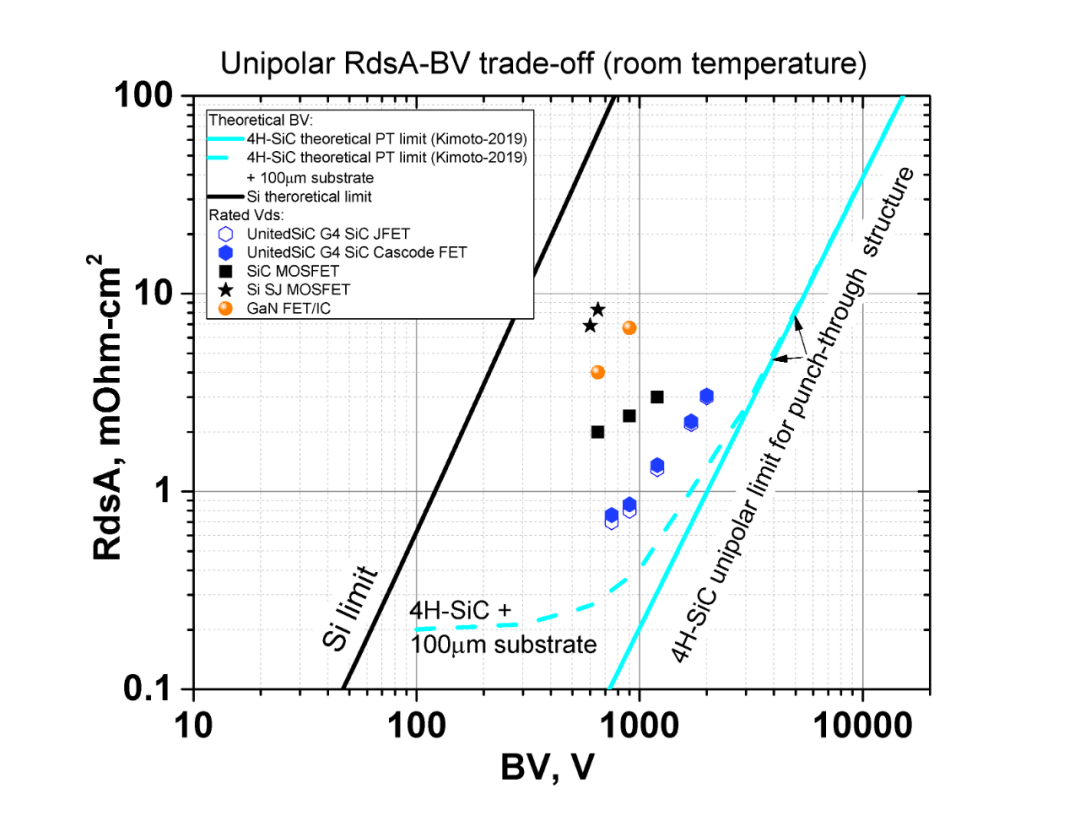
图1:2021年先进的硅和宽带隙开关技术的RdsA与电压额定值对比
图2显示的是本文中讨论的封装选项。TO247-4L是使用范围很广的TO247封装的变体。D2PAK-7L是表面安装式封装,很适合与碳化硅器件一同使用。穿孔式TO247凭借外露的大铜片可以散发掉更多功率。鉴于需要维护大爬电距离,D2PAK-7L晶粒垫相对较小。表1显示的是相对参数的对比,包括典型的封装电感、热垫大小(与散热器相连的铜面积)、爬电和间隙。
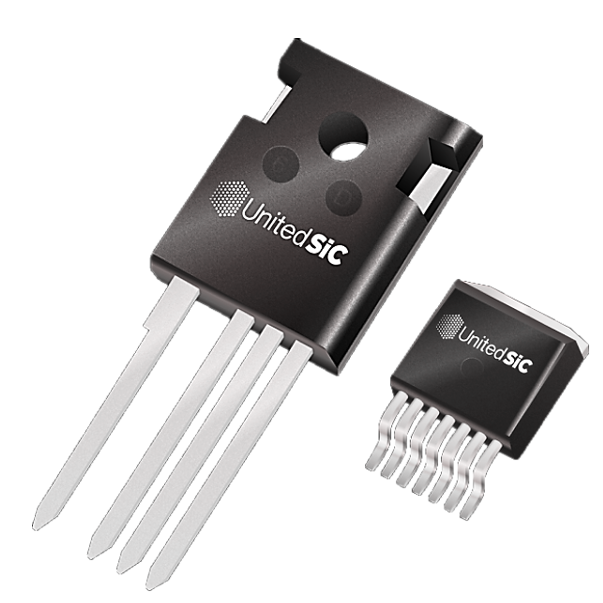
图2:TO247-4L(左)和D2PAK-7L(右)是广受欢迎的封装,是可用于车载充电器的穿孔和表面安装式选项
使用SMT器件可简化和提升制造自动化。因此,在电动车液冷环境中,将在绝缘金属衬底(IMS)上使用D2PAK-7L的选项作为TO247-4L替代方案是非常值得分析研究的。
由于分析功率损耗和温度峰值上升需要器件导电损耗数据、开关损耗数据和热阻数据,我们要先检查它们。然后使用FET-Jet[3]在线计算器来求得最差的工作损耗和温度升高,以检查所选器件和封装组合的可行性。
根据数据表曲线(参见图3a和3b),开关数据已经作为电流函数输入到计算器中,并考虑了所有器件的与温度相关的导通电阻。计算器中还提供了典型的最差情况下的热阻(RthJC)。接下来,我们看看模拟,以此指导对RthCA的合理评估,从而完成此分析所需的数据表。
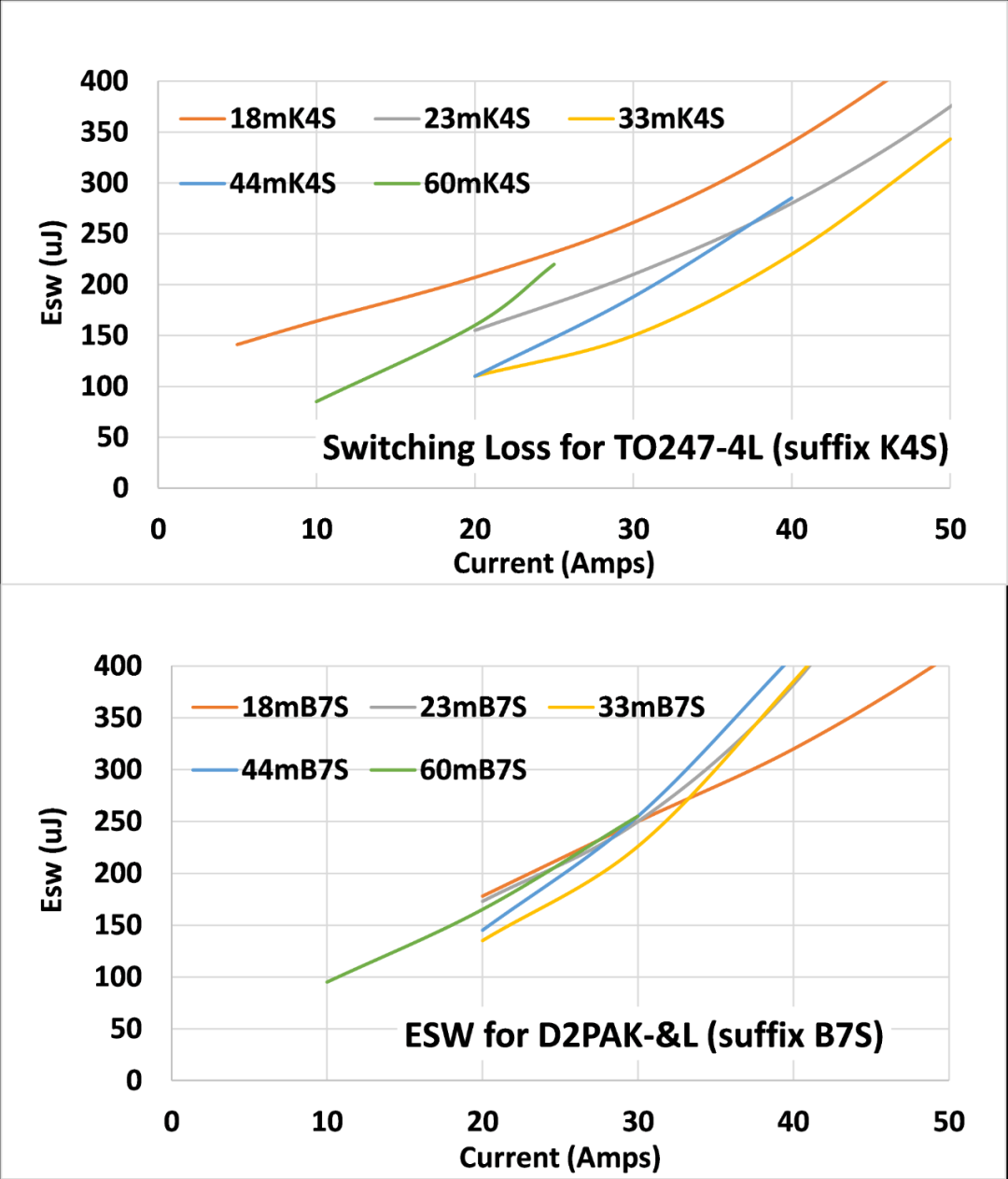
图3a(上)是TO247-4L 750V第四代SiC FET在400V总线下开关损耗与电流的对比。图3b(下)是这些器件在D2PAK-7L封装中的这些数据
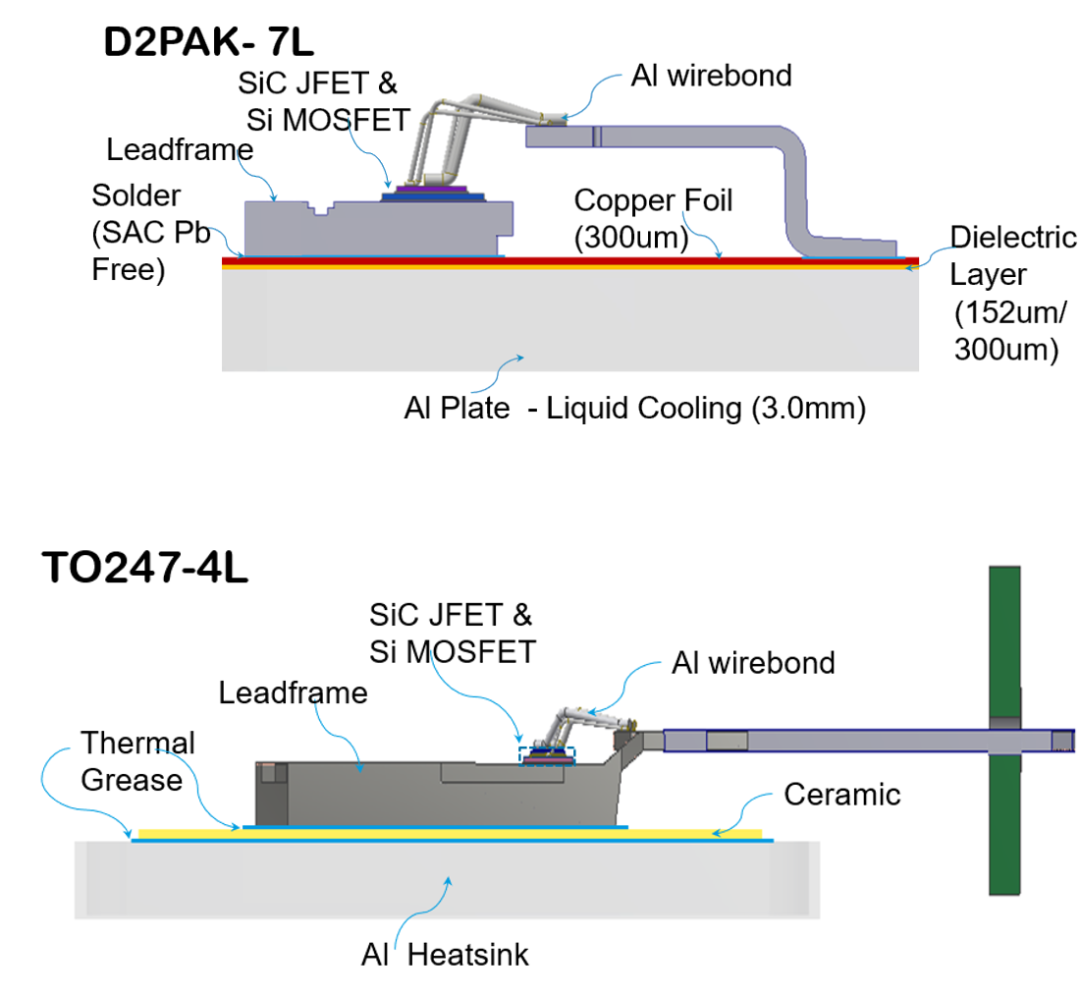
图4:TO247-4L和D2Pak-7L中从结到冷却液的热路径图
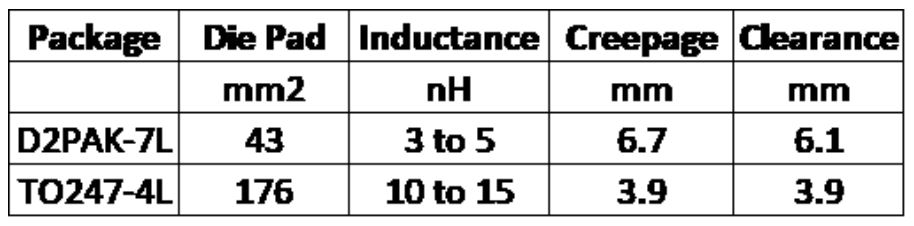
表1:图2中显示的两个封装的对比。SMT器件的电感明显更低,但是散热面积也较小
典型热环境的模拟对比
图4显示的是使用TO247-4L和在IMS上使用D2PAK-7L时图腾柱PFC的典型使用视图,表明了冷却功率电子器件所用的器件从结到冷却液的热流路径。表2a和2b总结了在一系列热界面(TIM)隔离选项下,各个器件的结到壳与壳到冷却液热阻。
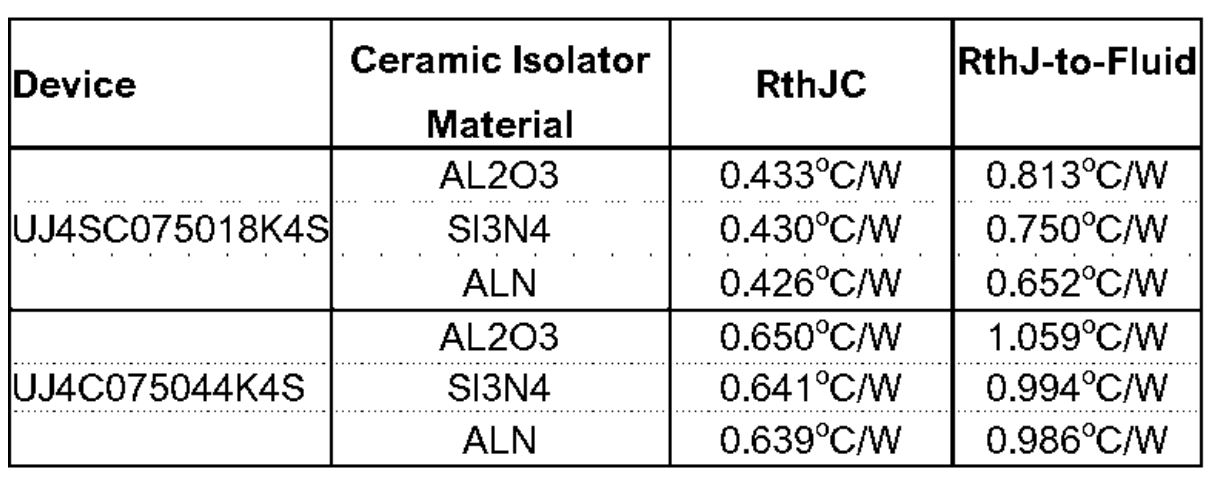
表2a:在安装到采用陶瓷绝缘体的冷却板上时,基于TO247的器件的热阻性能
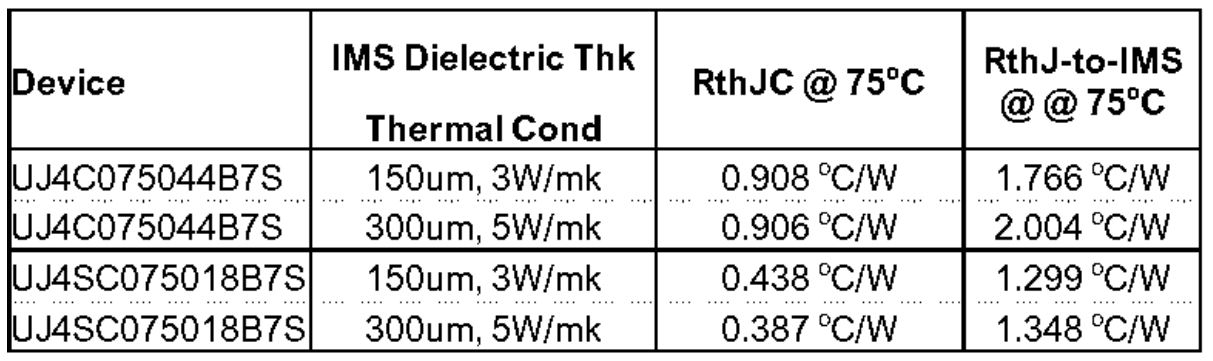
表2b:建立在IMS上的D2PAK-7L器件的热阻性能,其中的底部3mm Al采用液冷
根据这些结果,我们可以将0.6 °C/W作为TO247壳到冷却液的热阻的中间值,将1.2 °C/W作为D2Pak-7L的中间值,并将它们添加到结壳热阻中。虽然SiC FET的芯片体积小,但是可以通过银烧结式连接在封装中实现低RthJC。
案例1:400V总线系统的6.6kW(交流/直流)图腾柱PFC
图5显示的是图腾柱PFC拓扑的基本电路。表3汇编了此应用使用一系列第四代器件时在全负载和6.6 kW下的功率损耗和温度上升。其他电路条件有230 Vrms输入、400 V直流轨、75 kHzCCM模式开关、20% 电感纹波、散热器/液温80 °C、在相同封装类型的慢支路使用固定的11 mΩ,750 V器件、图腾柱PFC的两个交错快支路的各种器件[4]。我们可以看到一系列快支路选项,从18 mΩ到60 mΩ,并有Rds(on)极低的器件提供非常高的性能。该表显示的是每个快速支路FET在最差情况下的功率损耗、预计结温和半导体效率,这是仅功率半导体的效率损耗指标。即使壳到冷却液的热阻较高,达到1.2 °C/W,下表所示的表面安装式选项也是非常合理的选择。最后一部分决策可以基于设计中的整体热、效率和成本约束条件。现在,许多器件选项都是由Qorvo提供的。
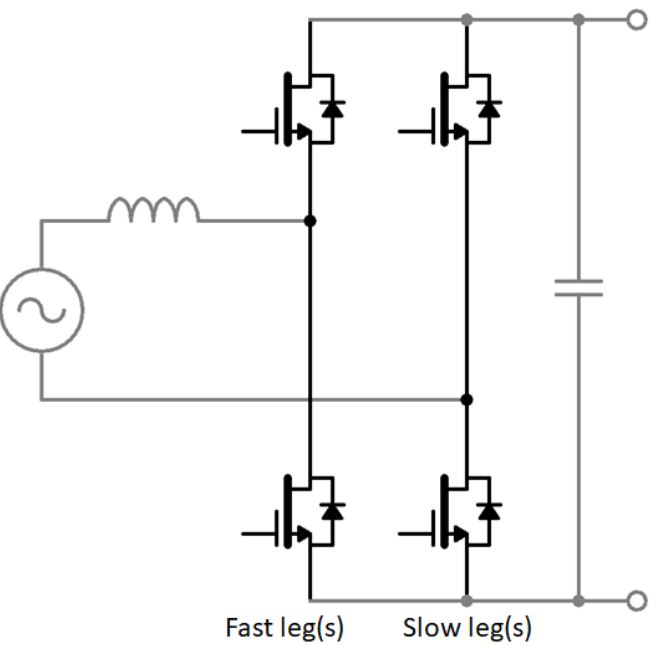
图5:本分析中使用的图腾柱PFC拓扑。我们假设两个交错的快速支路在每个位置有一个开关,在慢速支路中有一个低Rds器件
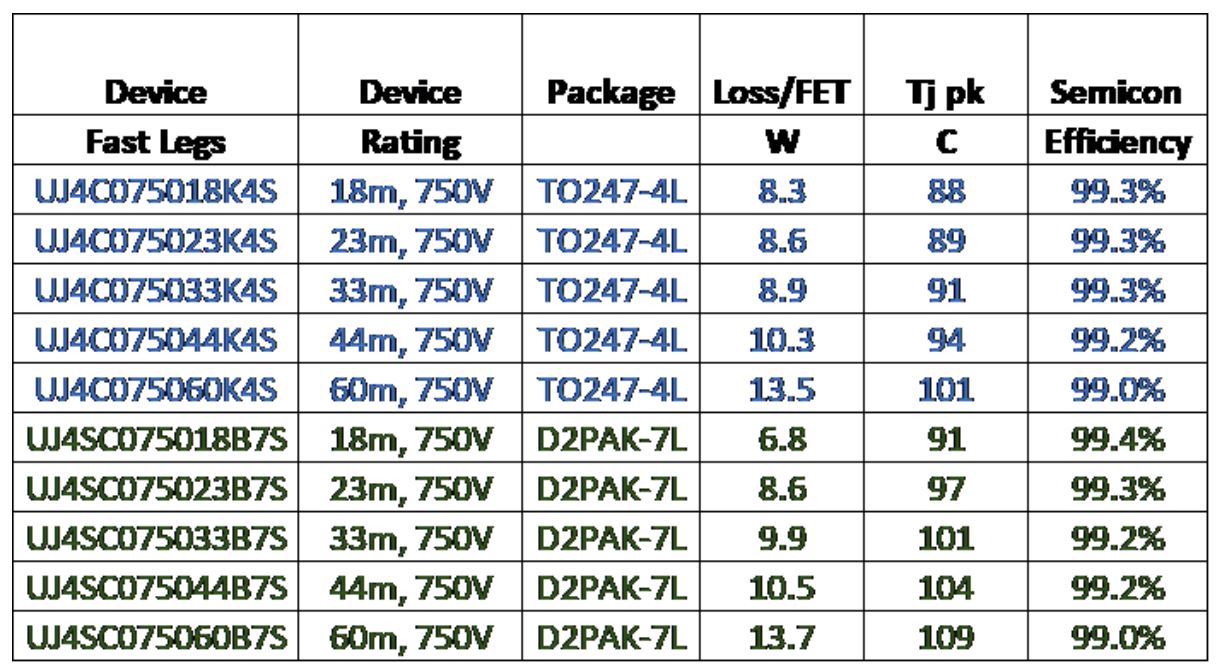
表3:各种第四代SiC FET选项的快速开关FET计算损耗、峰值结温和半导体损耗限制的效率。6.6 kWTPPFC在75 kHz下运行
案例2:400V总线系统的6.6 kWCLLC直流/直流
现在,我们可以考虑同一系列的器件在车载充电器的CLLC级中能提供什么。通常,由于器件不是硬开关,损耗会较低。我们假设此处使用全桥CLLC实施,如图6所示,并检查各个选项在6.6 kW、400 V总线、300 kHz开关频率和80 °C冷却液温下的功率损耗,我们还同样假设将0.6 °C/W作为TO247-4L的额外壳到冷却液热阻,将1.2 °C/W作为D2PAK-7LIMS的热阻。初级侧FET的计算损耗在表4中列出。
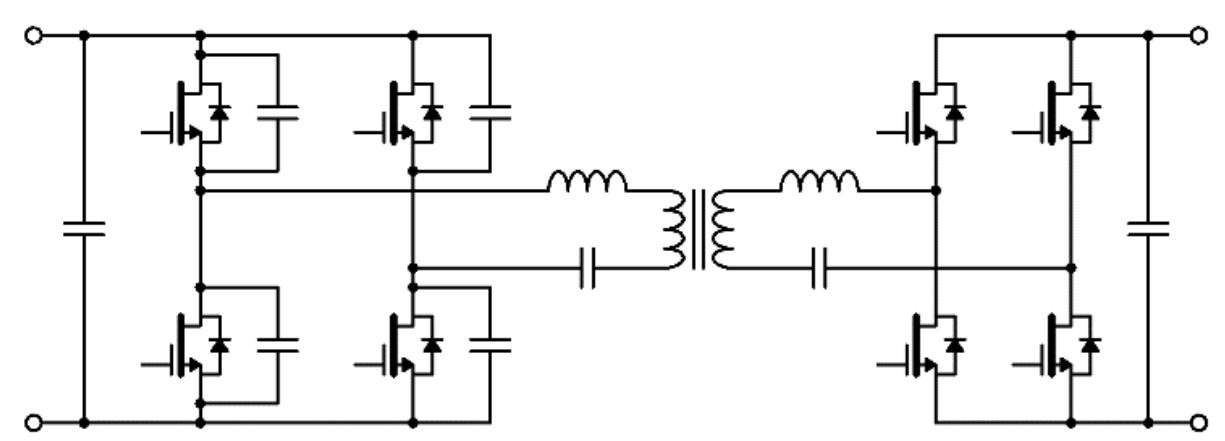
图6:表5中的估计所用的CLLC拓扑。考虑了初级侧FET。同样的器件通常也会用于次级侧
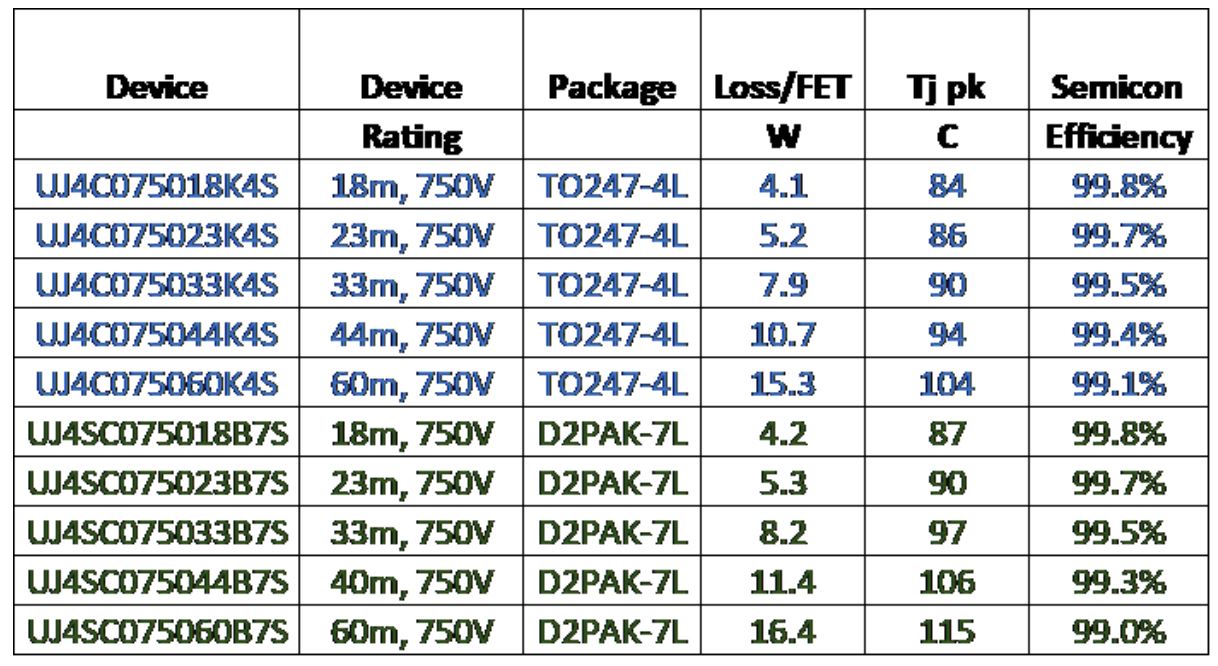
表4:各种第四代SiC FET选项的初级侧FET计算损耗、峰值结温和半导体损耗限制的效率。6.6 kW全桥CLLC在300 kHz下运行
在这种情况下,得益于LLC电路中的开关损耗接近零,虽然频率较高,但是开关损耗低得多。此外,有许多可行选项可供设计师们选择,包括适用于穿孔式和表面安装式的选项,让设计师们能灵活地优化性能、热管理、板空间和成本。SiC FET可以使用0至10 V驱动电压驱动且对性能没什么影响的特点也很有用,有助于限制驱动器损耗。
案例3:3: 22 kW Vienna整流器
最后一个有用示例是在22 kW Vienna整流器中使用750 V平台,如图7所示。对于这个3相电路,我们在假设使用750 VFET和50 A、1200 V UJ3D1250K2二极管的条件下执行计算。我们假设使用230 Vrms交流电输入、3相、800 V总线、40 kHz开关以及与之前示例中一样适用于穿孔式和SMT选项的壳到环境热条件。对于22 kW输入,RMS相电流约为31.9 A。
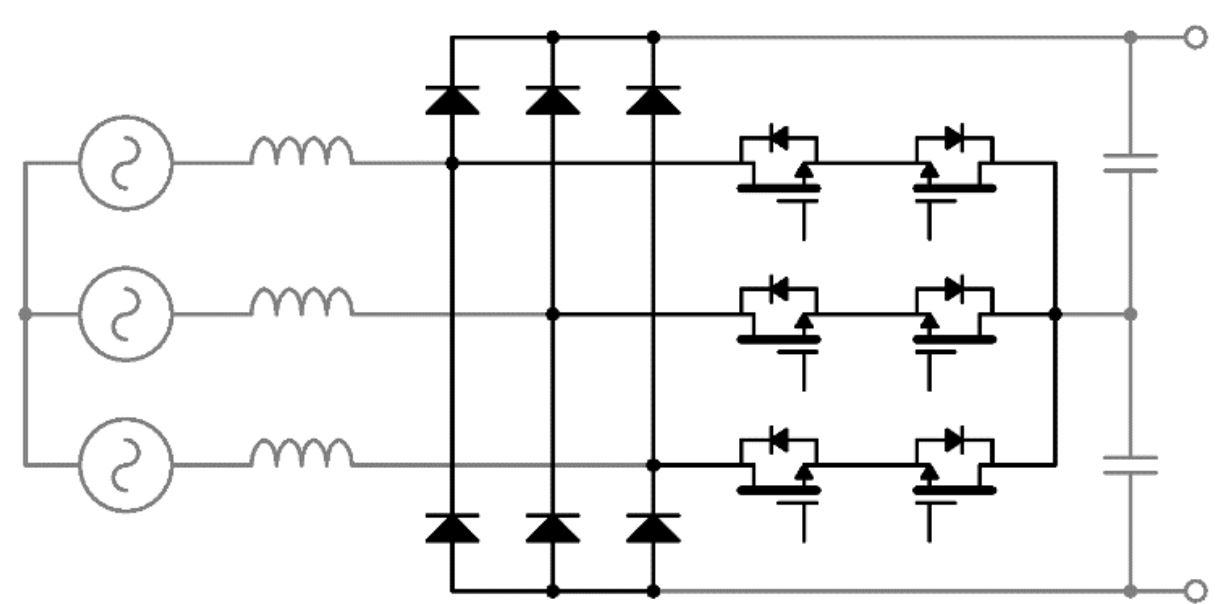
图7:全部使用SiC器件的Vienna整流器。二极管为1200 V SiC二极管,FET为第四代750 V SiC FET
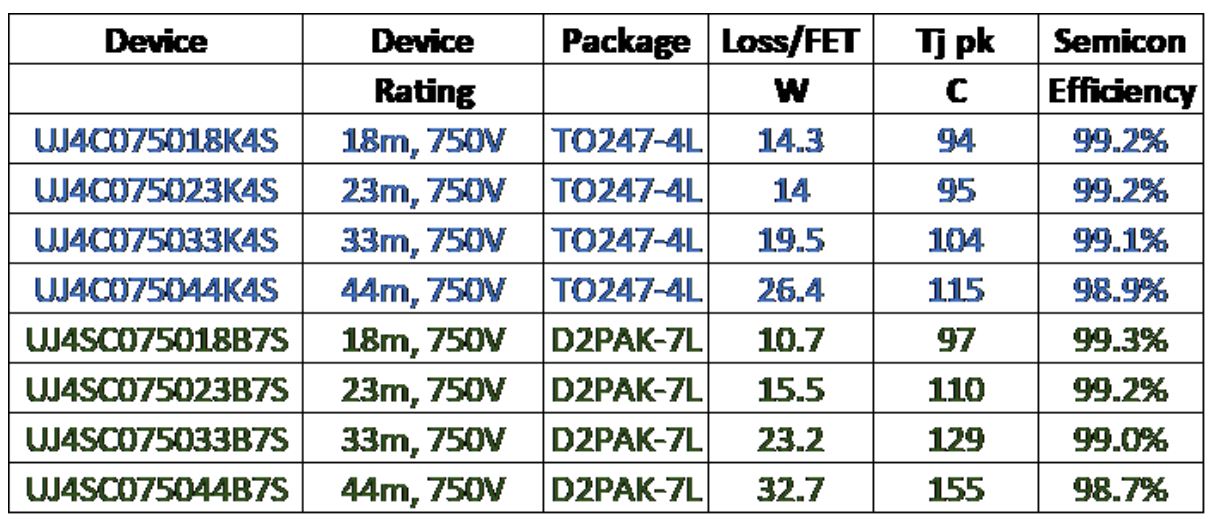
表5:各种第四代SiC FET选项的FET计算损耗、峰值结温和半导体损耗限制的效率。22 kWVienna整流器、800 V总线、40 kHz
在本案例中,TO247-4L封装中更高的散热能力发挥了更重要的作用,在使用电阻更高的器件时也有良好的热裕度。另一方面,18 mΩ至33 mΩ器件中的损耗极低,以至于在此功率电平下也可以采用表面安装式选项。
结论
第四代SiC FET的性能提升以及各种Rds(on)类在穿孔式和表面安装式封装中的可用性让设计师能不断改善车载充电器设计的效率、体积和废热,同时维持低成本。此外,使用较为简单的0至10/12/15 V栅极驱动可有助于管理成本和控制复杂性。
文章来源: UnitedSiC